This particular course entitled “Single-Phase Pipe Hydraulics & Pipe Sizing” under the specialization entitled “Design of Industrial Piping Systems” is mainly aimed at predicting the optimum pipe diameter of the piping system to meet the given process requirement when it is subjected to a single-phase fluid flow. Here, the piping system is either a single-path piping system or a multiple-path piping system. To achieve the single-point objective, i.e., the Sizing of the Ping System, essential concepts of single-phase fluid flow through pipes are covered, essential mathematical expressions are derived to understand the intricacy of the single-phase phenomena, and the importance of each term in governing equations is explained.

Give your career the gift of Coursera Plus with $160 off, billed annually. Save today.

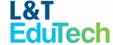
Single-Phase Pipe Hydraulics and Pipe Sizing
This course is part of Design of Industrial Piping Systems Specialization

Instructor: Subject Matter Expert
2,618 already enrolled
Included with
(27 reviews)
Recommended experience
Skills you'll gain
- 1. Knowledge of Fluid Mechanics, and Strength of Materials
- 3. Graduate students of Mechanical / Chemical / Petro-Chemical/ Instrumentation
- 4. Working professionals with B.Tech./B.E., in Mechanical / Chemical / Petro-Chemical/ Instrumentation
- 5. Diploma students of Mechanical / Chemical / Petro-Chemical/ Instrumentation
- 2. Undergraduate students of Mechanical / Chemical / Petro-Chemical/ Instrumentation
Details to know

Add to your LinkedIn profile
4 assignments
See how employees at top companies are mastering in-demand skills
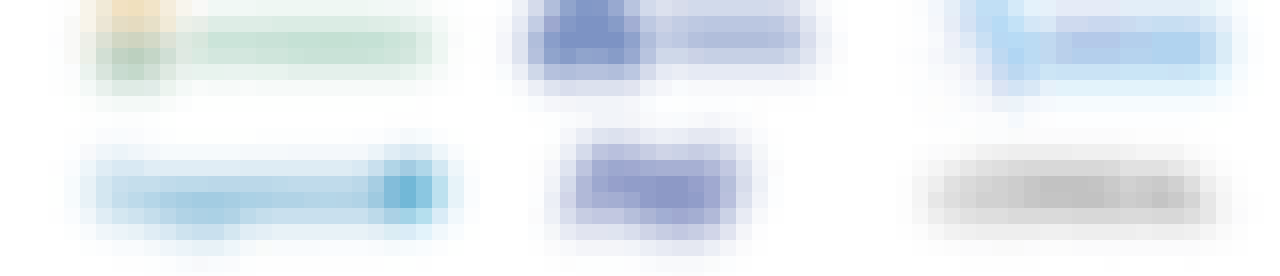
Build your subject-matter expertise
- Learn new concepts from industry experts
- Gain a foundational understanding of a subject or tool
- Develop job-relevant skills with hands-on projects
- Earn a shareable career certificate
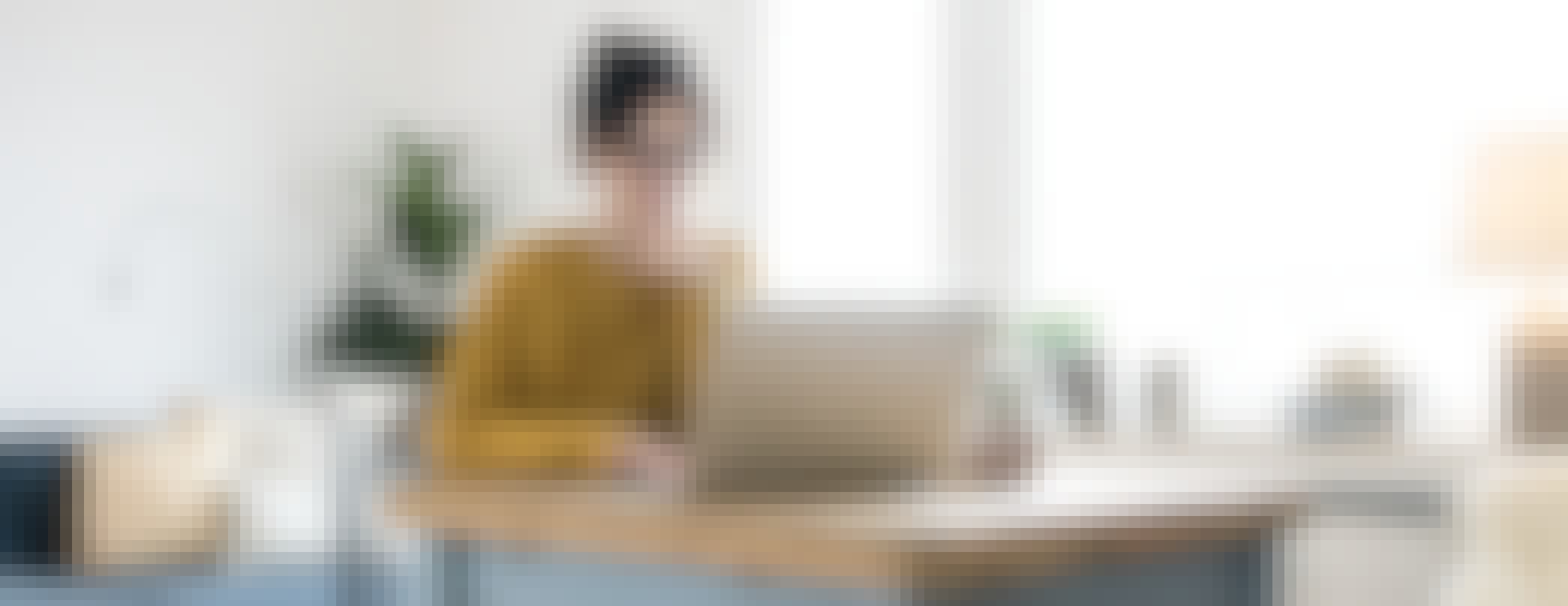

Earn a career certificate
Add this credential to your LinkedIn profile, resume, or CV
Share it on social media and in your performance review
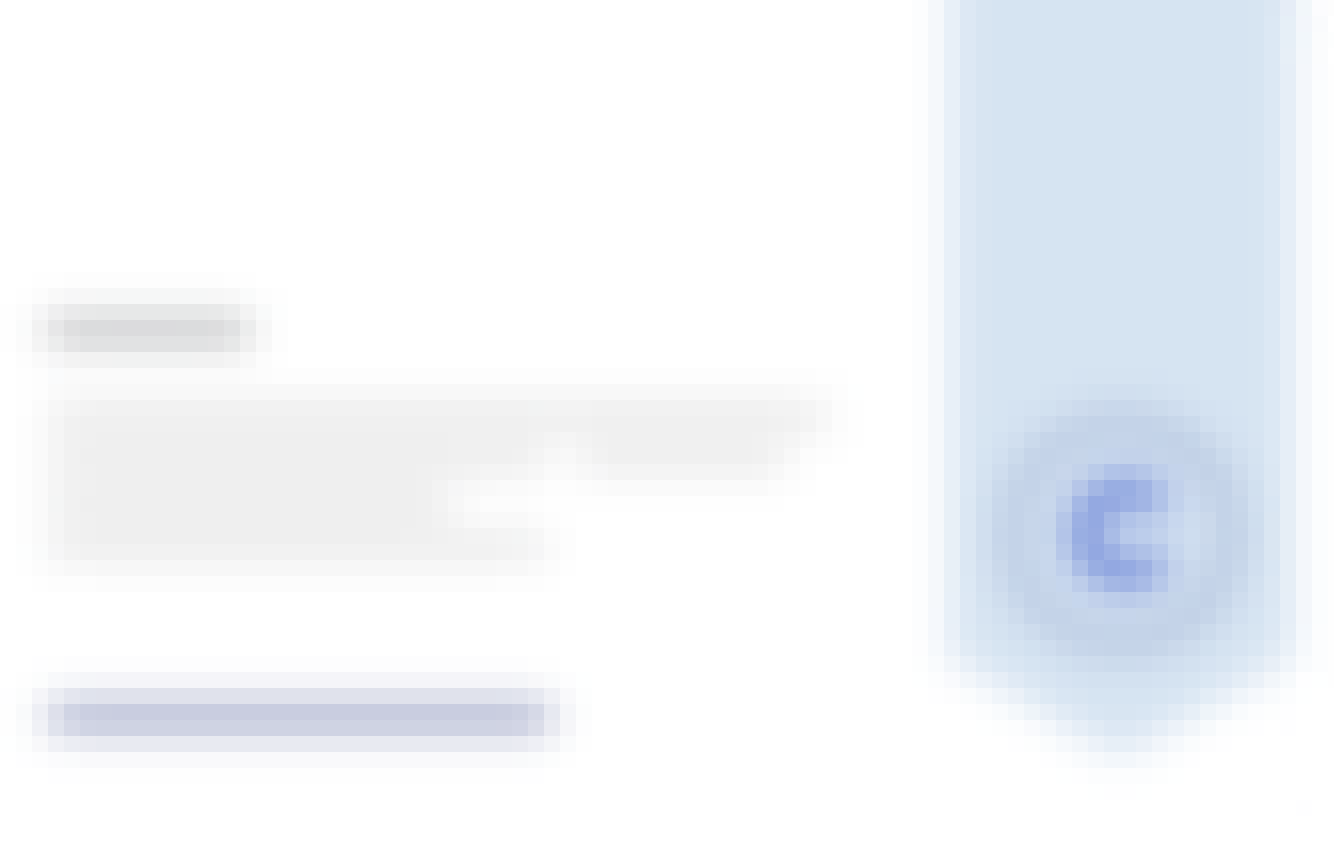
There are 4 modules in this course
This particular module started with the contribution of conduits in transporting different kinds of fluids starting from the fulfillment of day-to-day needs such as drinking water, cooking gas, etc., to natural gas, crude oil, petroleum products, etc. The phase of the fluid, classification of fluids based on compressibility and phase, and types of fluid flow such as internal, external, one, two, and three-dimensional are explained. The single-phase flow regimes that occur in a pipe when fluid flows, involved phenomena, terminologies, and necessary mathematical expressions are discussed. The concept of hydraulic radius, its determination for various geometry and configurations, and single-phase flow regime identification through the determination of Reynolds number are covered and demonstrated with the aid of practical problems. Derived the Bernoulli equation for an ideal fluid passing through a pipe, applied the steady state energy equation for a real fluid flowing through the pipe, compared both, and demonstrated how real fluids suffer the irreversible head loss, as well as Bernoulli equation gets modified when it is applied to a real fluid. A mathematical expression is derived to determine the irreversible head loss in known parameters introducing the Darcy–Weisbach friction factor. Head loss is also expressed in terms of the Fanning friction factor, bringing the relation among Darcy, Fanning, and Chisholm friction factors, and clarifying who prefers which friction factor during head or friction loss calculation. Friction factor correlation for laminar flow regime and various friction factor correlations including relative roughness term, both in explicit and implicit forms for turbulent flow are presented. Demonstrated the determination of frictional pressure drop for several practical problems. Finally, demonstrated the Moody diagram to get further insight into the single-phase phenomenon, the region where both pipe relative roughness and Reynolds number influence the friction factor, the region where only pipe relative roughness influences the friction factor for turbulent flow, and the regions related to laminar and transition flow regimes. Practical problems are solved using the Moody diagram to get acquainted with it.
What's included
20 videos1 reading1 assignment
This module deals with single-phase pressure drop prediction due to the presence of piping components like sudden enlargement, sudden contraction, orifice, nozzle, venturi, valves, and pipe fittings like bend, tee, etc., in a piping system. Mathematical expressions are derived for pressure loss due to eddie formation in turbulent zones created when the separation of fluid from the wall boundary takes place, and mixing of the fluid happens in the zone downstream of the pipe. The derived equations are functions of known parameters such as average fluid velocity either upstream or downstream and the ratio of upstream or downstream cross-sectional areas. Demonstrated the prediction of minor loss using the derived mathematical expressions by solving practical problems. Discussed the purposes of mounting the orifice in a pipeline in terms of metering the fluid and reduction of pressure drop to meet the process requirement even using multi-orifices configuration. Derived the mathematical expression to determine the permanent pressure drop caused by the presence of a sharp-edged orifice in the pipeline in terms of co-efficient of discharge and known parameters such as flow rate and cross-sectional areas of pipeline and orifice. To determine accurately the Non-Recoverable Pressure Drop, NRPD, the resistance coefficients are presented for ‘sharp-edged orifice’ and ‘thick-edged orifice’ (both straight and not straight). Mathematical expressions are derived for both the nozzle and venturi to determine the head loss across them. Standards used to manufacture the venturi meter, limits for converging and diverging angles, throat diameter range, and length are mentioned to maintain minimal head loss. Four possible outlet and inlet configurations to connect an outlet and inlet pipe to process equipment and head loss offered by them are covered. Determination of head losses offered by the commonly used valves in the process industry and pipe fittings such as bend, tees, crosses, etc., using both the ‘loss coefficient’ and ‘equivalent length’ methods is discussed. Advantages and limitations of Orifice, nozzle, venturi, and valves are discussed. Finally, demonstrated the head loss calculation of piping systems consisting of all “piping components”.
What's included
14 videos1 assignment
This module covers the prediction of single-phase pressure drops in piping networks since in most practical cases the fluid flow is through multiple paths where the fluid at the inlet node splits/branches into multiple flow rates and joins at the exit node. Three types of piping networks are considered, starting with parallel piping networks, and series piping networks to get acquainted with solving simple piping networks to further solve complex piping networks which are a combination of parallel and series piping networks. Next, complex piping networks which are a combination of both series and parallel piping networks are covered. Demonstrated the fluid flow rate through each branch of the parallel piping network between the inlet and exit nodes. As the inlet and exit nodes are common to each of the branch piping systems, the fluid pressure drop in each branch piping system is the same, as a result, the flow resistance in each branch piping system is different and hence the fluid flow rate in each branch also different. Demonstrated the percentage of total fluid flow rate in each branch is unaltered with change in inflow fluid rate in case of parallel piping network. To solve complex piping networks ‘Hardy-Cross Method’ is introduced. Demonstrated the steps involved in solving the complex piping networks using ‘Hardy-Cross Method’ and provided solutions to different complex piping networks. Next, a mathematical expression is presented to determine the head loss in a header, and prediction of head loss in the header considering practical problems is demonstrated. Finally, explained what is a branching piping system and demonstrated how to predict the fluid flow rates and their directions in branching pipes.
What's included
13 videos1 assignment
This module exclusively covers the important aspect of fluid flow in pipes, i.e., analysis of transient flow in pipes and the effect of transients in the safe operation of the piping system. A piping system undergoes a transient state during startup, shutdown, emergency, external disturbances, accidental scenarios, and upset conditions. A one-dimensional mathematical expression is provided for transient incompressible fluid flow. Explained what is an oscillatory transient, and derived the governing equation to capture the dynamic behavior of oscillatory fluid flow. Discussed what is water hammer, the causes of a water hammer, and the extreme effect of a water hammer on a piping system and pipe supports. Discussed the pressure wave propagation along the length of the pipe due to the stopping of the fluid flow. Pressure wave propagation time and disturbance time are discussed. Demonstrated the identification of the type of transients such as water hammer or surge by comparing propagation time and disturbance time. Covered the calculation of the speed of the sonic pressure wave through the liquid considering pipe as rigid as well as elastic. Also, the determination of pressure rise and drop, and the force exerted on the wedge or disc of the valve due to the slow closing and opening of the valve is covered. Mathematical expressions are provided to determine the pressure rise and drop due to the sudden closing and opening of the valve and demonstrated. Discussed the impact of a spike in pressure due to the sudden closing of valves on the safe operation of the piping system, and how to protect the piping system from water hammer. Explained the effect of the change of phase from single-phase to two-phase, and provided the equation to determine the velocity of sound in the liquid-vapor mixture. Explained the possibilities for the steam-hammer occurrence, and demonstrated how a piping system is subjected to steam-hammer through a practical case. Explained the limitation of the Hazen-Williams equation in solving gravity-driven liquid flow, and provided Hazen-Williams, Manning, and Darcy-Weisbach equations in terms of pipe slope which can be applied to gravity-driven liquid flow through sloped pipes and demonstrated the design. Discussed the importance of partially filled liquid flow under gravity through a sloped pipe over a filled sloped pipe with liquid flow and demonstrated how to design a sloped pipe for partial liquid flow.
What's included
15 videos1 assignment
Instructor

Offered by
Recommended if you're interested in Mechanical Engineering
DeepLearning.AI
Starweaver
Coursera Instructor Network
Why people choose Coursera for their career




Learner reviews
Showing 3 of 27
27 reviews
- 5 stars
66.66%
- 4 stars
25.92%
- 3 stars
0%
- 2 stars
3.70%
- 1 star
3.70%

Open new doors with Coursera Plus
Unlimited access to 7,000+ world-class courses, hands-on projects, and job-ready certificate programs - all included in your subscription
Advance your career with an online degree
Earn a degree from world-class universities - 100% online
Join over 3,400 global companies that choose Coursera for Business
Upskill your employees to excel in the digital economy
Frequently asked questions
Access to lectures and assignments depends on your type of enrollment. If you take a course in audit mode, you will be able to see most course materials for free. To access graded assignments and to earn a Certificate, you will need to purchase the Certificate experience, during or after your audit. If you don't see the audit option:
The course may not offer an audit option. You can try a Free Trial instead, or apply for Financial Aid.
The course may offer 'Full Course, No Certificate' instead. This option lets you see all course materials, submit required assessments, and get a final grade. This also means that you will not be able to purchase a Certificate experience.
When you enroll in the course, you get access to all of the courses in the Specialization, and you earn a certificate when you complete the work. Your electronic Certificate will be added to your Accomplishments page - from there, you can print your Certificate or add it to your LinkedIn profile. If you only want to read and view the course content, you can audit the course for free.
If you subscribed, you get a 7-day free trial during which you can cancel at no penalty. After that, we don’t give refunds, but you can cancel your subscription at any time. See our full refund policy.